Manufacturing:
- Separate Facilities for Subsystems and Units, Amplifier Modules, DROs and Mixers, and Passive Filter Assemblies
- 10,000 sq.ft. Class 10,000 Clean Rooms
- For Hybrids, Automatic Wire-Bond and Epoxy Dispense facilitates high thru-put and performance and quality repeatability
Active Module Screening: All RF Electronic Hybrid manufacturing and screening is performed in-house, including manufacturing, bake out and seal, fine and gross leak detection, thermal cycling, burn in and accelerated life testing, constant acceleration, PIND, and pre and post RF characterization; IAW MIL-PRF-38534 class K requirements and Mil-Std 883 methods, tailored per Lucix operating procedures.
QCI: For Hybrid QCI testing; outside NASA-certified facilities utilized for RGA and DPA.
10,000 sq.ft. Class 10,000 Clean Rooms
In-Line Quality:
Lucix uses Optical Leak Testing defined in MIL-STD-883 method C4/C5. This testing is a laser inferometry method that combines fine/gross leak testing, does not require immersion in hot fluid and allows individual parts to be measured simultaneously. This yields accurate testing with increased capacity. Additionally, this test can be performed in-situ for evaluating hybrids already incorporated into higher level assemblies.
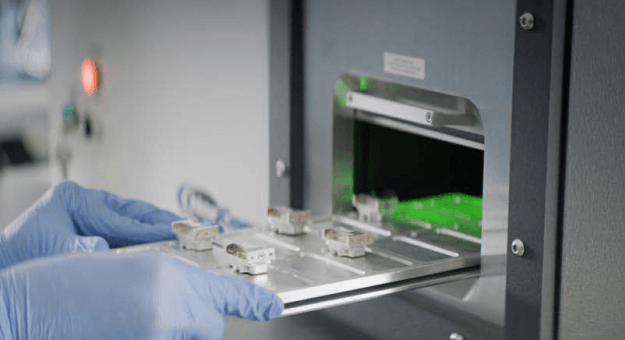
QCI: For Hybrid QCI testing; outside NASA-certified facilities utilized for RGA and DPA.
Lucix environmental laboratories provide multiple thermal test chambers for component burn-in, thermal cycling, accelerated life testing and vibration. Extended level vibration and Shock facilities are utilized for both qualification and acceptance screening as required. Thermal vacuum facilities are utilized as required for qualification and acceptance testing of Space hardware.
Incoming Material Quality: All incoming material is thoroughly inspected and screened. Mechanical parts are verified using automated VMM (Visual Measurement Machine) to ensure proper machining and fit. Chemical composition on mechanical and electrical components is checked using XRF (X-Ray Fluorescence) to ensure drawing compliant and screen out prohibited materials and finishes. Other mission critical materials are screened through bonding, soldering, and other commodity specific testing before placing into flight stock. All these test and inspections ensure quality parts that yield high quality assemblies.;
Test
Substantial investments in laboratory and test equipment enables Lucix to develop and qualify any combination of payload types simultaneously. This in-house capability has led Lucix to become a preeminent satellite communications company with the engineering talent and through-put to match.
All components and subsystems are tested in Lucix facilities and under-go rigorous qualification and environmental screening to ensure mission success.

-
Test Facilities For LNAs, Converters, Receivers, Reference Generators / MLOs / MROs, Power Monitors, CPSUs
- Thru-put: >100 units per month.
- 10 MHz to 67 GHz Measurement Range
- Multiple Vibration, Thermal Cycle and Burn-In Stations
- State-of-the-Art Phase Noise Measurement Capability / Screen Room
-
Nine State-of-the-Art Thermal-Vacuum Test Stations
- Stations test up to 24 RF chains simultaneously in thermal-vacuum conditions. Net thru-put: up to 170 units / RF chains per month.
-
Two vibration tables
- Equipped for either power-off, or power-on with DC and RF monitoring
-
For Qualification special tests
- Multiple outside facilities for full EMI/EMC and Pyroshock testing
-
High Power special tests
- High-Power Component and Integrated Assembly Testing – for Multipactor, Corona Effects, and PIM (Passive Intermodulation)